図1:超音波探傷技術と流れ場分布計
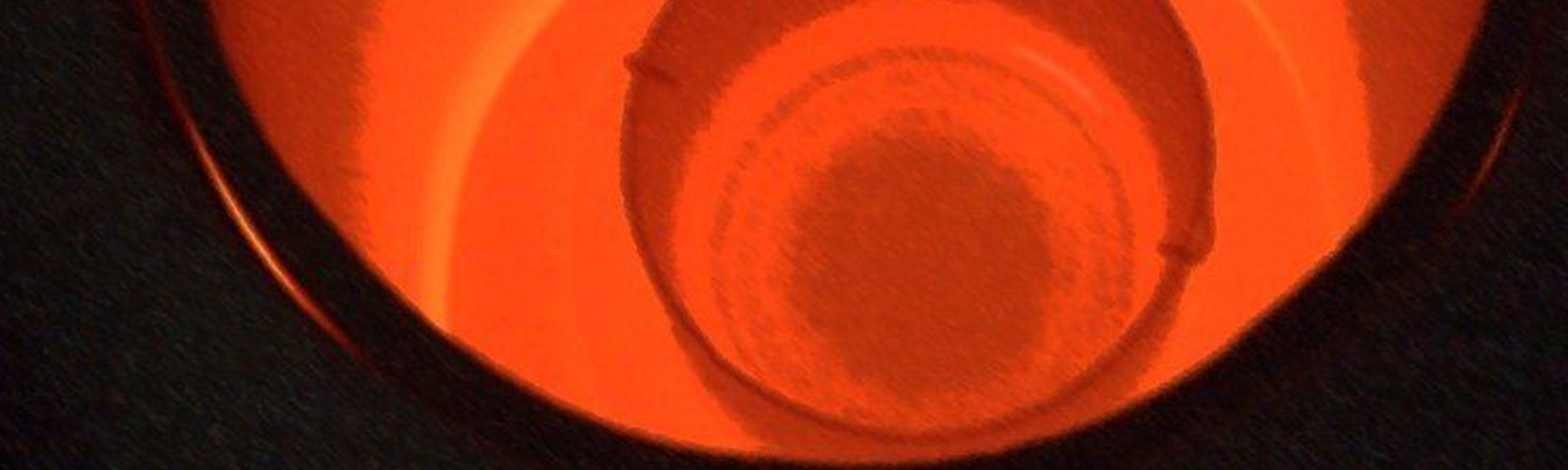
研究内容
About Us
超音波、レーザー、電気伝導、画像処理を用いた 先進的計測・診断技術の開発
○研究概要
超音波、レーザー、電気伝導、画像処理等を用いた非破壊検査技術や流体計測技術、診断技術の開発を行っています。以下に、当研究室で扱っている計測・診断技術に関するいくつかの研究例の詳細を挙げます。
[超音波計測・診断技術]
○高時間分解能を持った流速分布計測アルゴリズムUTDCの高度化
○2波長超音波計測手法(2相物質、流体計測への試み)
○スイッチング、あるいは、複数センサを用いた副測定線計測手法
○流速・流路断面同時計測技術
○フェイズドアレイ超音波計測技術
○超音波探傷技術と流れ場分布計測の複合化計測
○空中超音波流体計測システム開発
上記、研究テーマの中から、フェイズドアレイ超音波計測手法、超音波探傷技術と流れ場分布計測の複合化計測、空中超音波流体計測システム開発について紹介します。
従来から原子炉溶接部配管の疲労亀裂や応力腐食割れ等の探傷技術に超音波探傷が利用されてきています。特に近年、1つのセンサに複数個の素子を連続的に埋込んだアレイセンサを用いて、アレイセンサ内の各素子に遅延を掛けて振動させることにより、音響ビームを集音させたり、任意角度で発信させたり出来るフェイズドアレイ探傷法が注目を集めています。この手法を用いる事により、従来困難とされていた位置にある溶接箇所や亀裂部分の診断が可能となってきました。ところで、原子力分野においては事故が発生する場合には流体要素が絡んでいることが多く、配管の疲労度合を超音波探傷で計測するだけではなく、その配管の内部の流れ場を同時に取得しておくことは大変重要となります。そこで本研究室では、従来からある超音波流速分布計測法の高精度超音波流量計にフェイズドアレイ法を用いた診断技術を融合して、配管壁内の探傷を行いながら、流れ場の流速分布計測が可能なフェイズドアレイ探傷式超音波流速分布流量計の開発を行っています。以下に、超音波探傷技術と流れ場分布計測の複合化計測の概要図を図1、フェイズドアレイを用いた超音波流速分布計測手法の概要図を図2に示します。リニアアレイセンサ、および、計測システムの写真を図3、図4に示します。
また、空中超音波を用いて非接触にて流速分布が計測できる新しい超音波流速計を開発することを行っています(図5、図6)。具体的には,超音波センサを接液せずに空中に保持したまま,液体内にパルス超音波を入射し,流体内に懸濁している微粒子などの反射体からの微量なエコー信号を,特性プリアンプで増幅するとともに,連続する2波以上の繰り返しエコー信号を用いて時間領域相関法にて微粒子の反射時間を特定し,繰り返し時間と位置から微粒子の速度を算出する方法を用いて,パルス波発信方向の速度分布を計測することを考えています。本手法は、従来計測困難とされている高温の流れ場への適用が期待されています。
図3:リニアアレイセンサ
図4:フェイズドアレイ超音波計測システム
図5:空中超音波流体計測システム概要
図6:開発中の空中超音波流体計測システム写真
[可視化計測、レーザー計測、画像処理計測診断技術]
○レーザーライトシートを用いた可視化
○PIV,PTV
○LDV
以下は、内円筒が回転し、外円筒が固定されている同心二重円筒間において発生するテイラークエット渦流れを対象として、流れに混入させたアルミ微粒子をトレーサーとして、レーザーライトシートを用いた可視化法によりその断面の渦構造を可視化し、また、同時に、超音波流速分布計によって、その渦流れの速度分布を計測した際の一例を示しています(図7)。青色の写真がレーザーライトーシートによる渦流れの可視化例、その右に並べられているグラフが超音波流速分布計測計によって得られた速度分布例を示しています。これら光学的な可視化や超音波による可視化計測技術を用いることで、容器内部での流れ場が明確に捉えらます。この例では円筒間のギャップにおいて4個の渦が発生していることが判ります。
図7:レーザーライトシート可視化と超音波による流体計測の例
(対象とした流れ場:テイラークエット渦流れ)
[電気伝導を用いた計測・診断技術]
○円管、矩形管内ワイヤーメッシュ計測
○ワイヤーメッシュ法を用いた気液2相計測
○管面設置型ワイヤーメッシュ計測(流れへの影響が少ない壁面設置型ワイヤーメッシュセンサの開発)
○マイクロワイヤーメッシュ計測(空間分解能向上に関する研究、また、マイクロ流れ計測への試み)
以下は、管面設置型ワイヤーメッシュ計測技術に関する紹介です。混相流における流体間の電気伝導の差異を利用した流動計測の歴史は古く、プローブ法などの多くの手法が開発され、二相流動構造の解明のために適用されてきています。そのような中、流路断面に電極ワイヤーを張りめぐらせ、それらの交点における電気伝導率計測から、2次元ボイド率分布計測を可能とするワイヤーメッシュセンサ(WMS)を用いた気液二相流計測が注目されてきています。WMSは、流路断面におけるボイド率分布計測に加え、得られたデータから気泡径分布や気泡速度分布の算出が可能であり、近年では、高温・高圧条件下や大口径管内流動への適用性が示されており、気液二相流動の解明に対して非常に有効な手法です。しかしながら、電極を流路内へ挿入する手法のため、流れ場への影響が無視できず、センサを通過する気泡に対して分裂効果や速度変化効果を与えることが示されています。
そこで、WMSの電極配置方法を変更することで、電極による流れ場への影響を極力少なくし、流路間隙におけるボイド率分布を計測するマイクロワイヤーメッシュセンサ(micro Wire-Mesh Sensor; μWMS)を考案しています。
本手法は、2つの流路壁に挟まれた狭隘流路への適用に限られるが、複雑な流路形状を有する稠密炉心内流動計測やマイクロ流路内計測への適用が可能であると考えられます。ボイド率分布および可視化計測との比較のため、平行平板間における瞬時ボイド率の2次元分布,および高速度カメラによって得られた同時刻における撮影画像を図9に示します。ボイド率分布において,気泡が形状を変化させながら上昇していく様子が捉えられていることがわかります。また、画像との比較より、その形状が正確に計測できていることが確認できます。
また、得られた2次元ボイド率分布に対して、ボイド率のしきい値を用いることで、気液相の分離を行い、気相のみを抽出することができます。そして、その気相分布から気泡の3次元形状の再構築を行うために、複数の気相が流路間隙方向に存在しない、気相が流路間隙中央を流れる、という仮定を用いますと、計測されたボイド率を流路隙間に対する気相の厚みとしてみなすことができます。図10に3次元気泡分布の算出例を示す.気泡の位置,大きさに加えて,その形状が可視化できています。また、このような3次元分布より気泡の体積の算出が可能になると考えられます。
図8:管面設置型ワイヤーメッシュ計測
図9:ボイド率分布(左)および可視化計測(右)との比較
![]() |
![]() |
(a)小さな気泡 |
(b)大きな気泡 |
図10:三次元気泡分布
○主な連携機関
室蘭工業大学、東工大原子炉研、ETH(スイス工科大学)、ジャパンプローブ